Explore What We Can Do For You
Innovative Manufacturing Solutions for Advanced Medical Devices
Atalys is a leading vertically integrated medical device manufacturing platform with comprehensive end-to-end services, cutting-edge technology, and expertise across the entire production process. We are dedicated to enhancing patient care and improving health outcomes by producing highly engineered components and extreme precision parts of the highest quality and reliability for the most critical surgical applications.
Cost Effective Automation and Low-Cost Assembly Options
As a strategic partner of our customers, we constantly strive to optimize production efficiency and reduce overall manufacturing costs by leveraging advanced robotics and automation technologies, as well as alternative nearshore assembly locations.
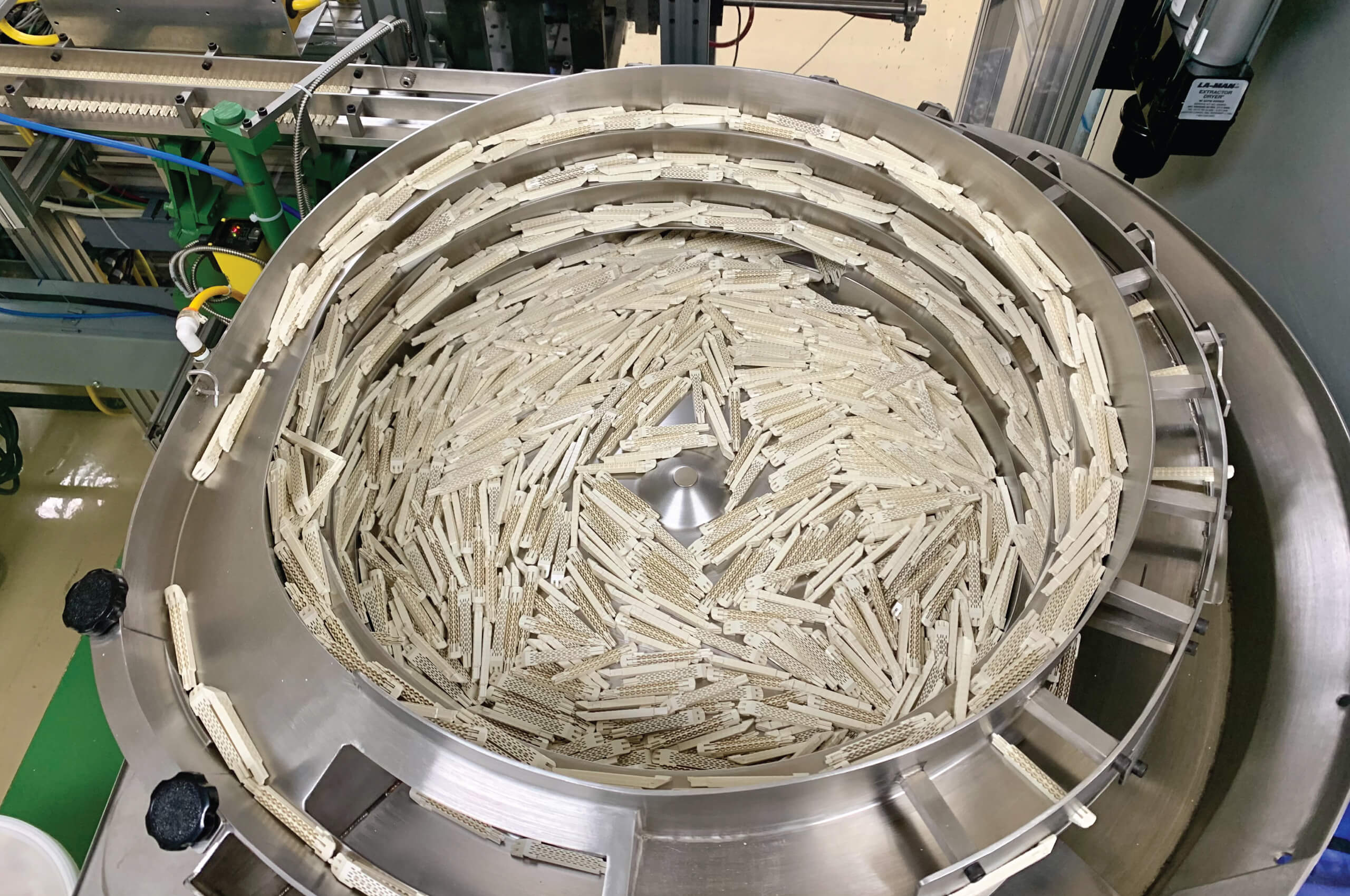
WHY WORK WITH US
We make the impossible, possible.
Experienced Engineering Team
Our DFM capabilities are proven and second to none in the industry.
Our engineering teams are staffed with highly educated and experienced professionals, several of whom have advanced degrees who can engineer around normal tooling constraints to develop the best possible solution for your part.
We are an established leader in extreme precision and complex geometry tooling.
We have 500+ years of in house mold making experience on the floor and are experts in high tolerance molds, complex tool geometries, various mold actions and tooling options for every need.
Unrivaled Tooling Expertise
Medical Device Manufacturing Mastery
We have proven “bookshelf” technologies designed and built
in-house, or under the expert guidance of our team.
We possess the knowhow and expertise to reliably develop, build, and run fully-automated manufacturing systems for specialized components through a single supply chain, reducing risks and lowering costs.
We bring simplicity to highly
complex manufacturing
programs.
Our highly experienced and skilled Program Management teams provide exceptional project management depth and insights that simplify highly complex projects to ensure timely completion and delivery.
RELIABLE PROGRAM MANAGEMENT
Case Studies From Our Recent Work
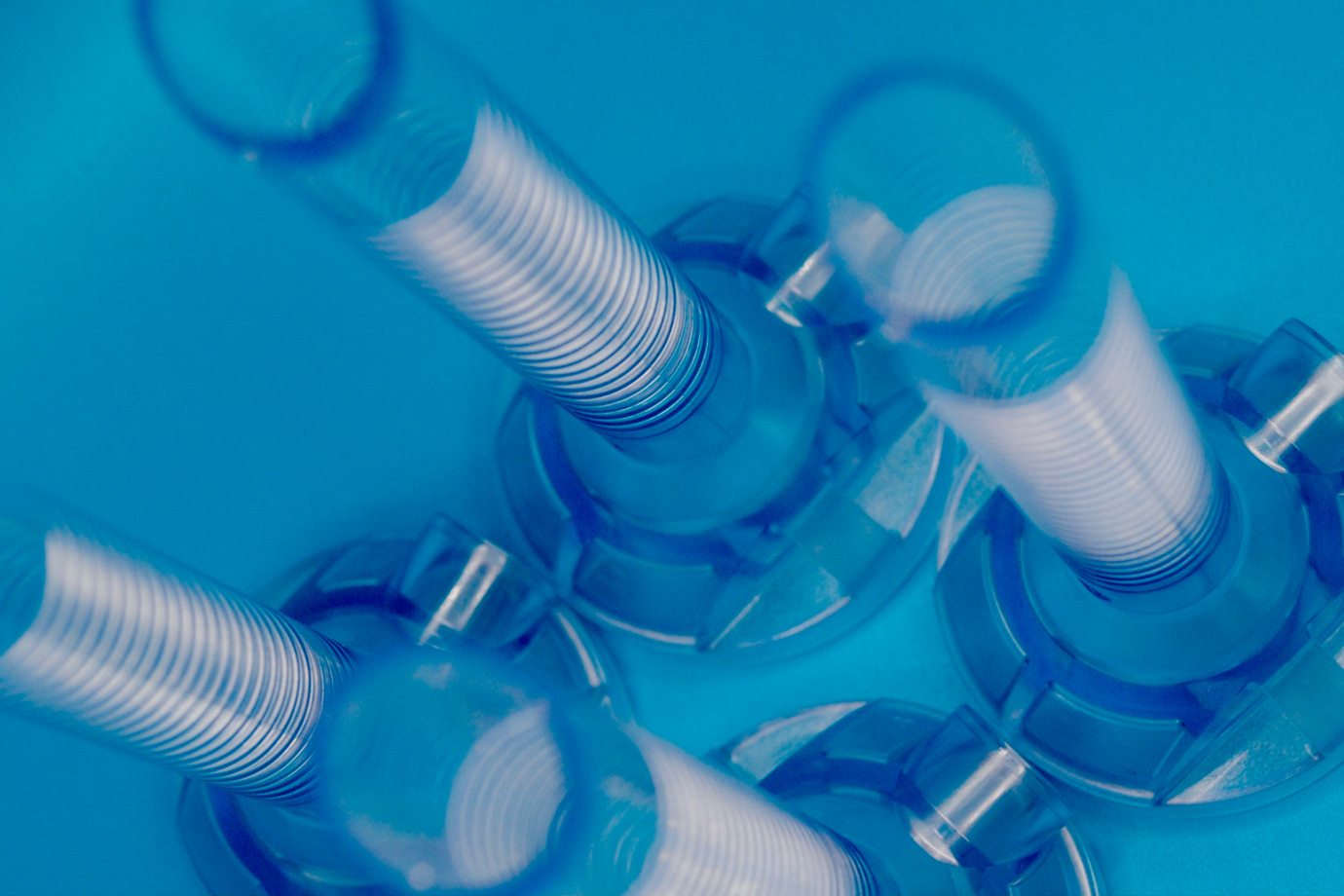
SURGICAL ACCESS
Long Cannula Cooling Challenge
A customer came to us with a cooling challenge involving a long cannula. The parts were coming off the press at high temperatures that rendered them unusable. As a short-term measure, the parts were kept longer in the mold to give them extra time to cool. This lengthened cycle times, however, and was far from sustainable. Find out how Atalys engineers came up up with a long-term, viable solution in this case study.
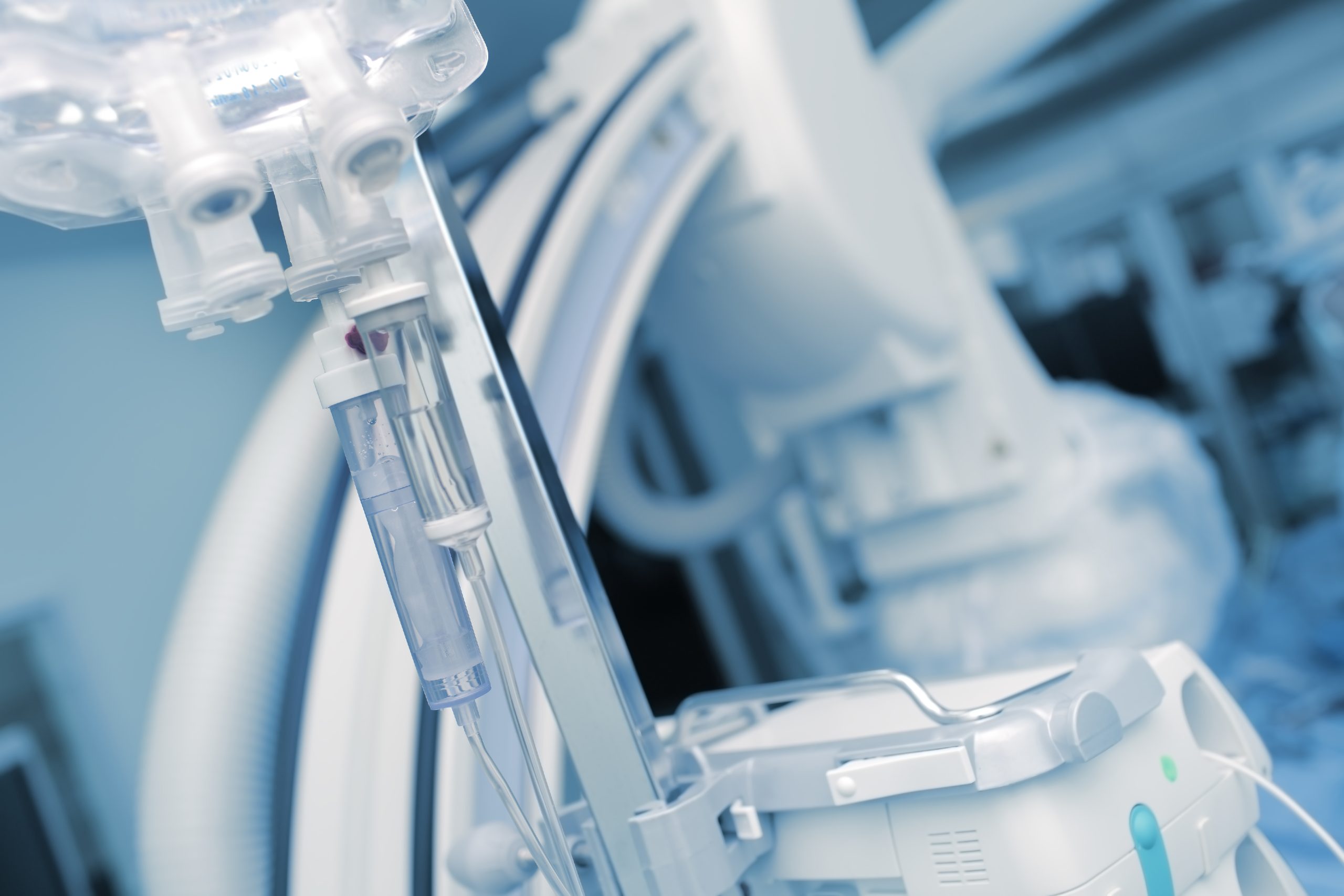
FLUID IV AND DRUG DELIVERY
Molding Tubes With No Draft
Medical device parts with cylindrical shapes are traditionally designed to have tapers in both internal and external walls which facilitate easy ejection of the molded part from the tool without any issues. There are times, however, when a part’s required tolerances and/or function will not allow for it. This was the case with a customer who wanted a tubular component molded without drafts under strict tolerances. Could the part be molded without any drafts? Find out in this case study.
ATALYS BY THE NUMBERS, 2024
Four Human Lives Touched Per Second
Experience and Expertise that Transcend Industries
Beyond Medical Devices
Our extreme precision tooling and advance engineering capabilities not only cater to life-saving medical technologies, but are exceptionally agile to be adapted to demanding consumer, industrial, aerospace and defense markets.
Whether we are working on groundbreaking medical devices or high-precision components for consumer, industrial, or aerospace and defense applications, we staff every project with an expert interdisciplinary team from tooling design and engineering to manufacturing operations and quality assurance, allowing us to optimize production while adhering to the most stringent specifications.
So if your mission is to save lives or simply make them better, our unwavering pursuit of innovation, efficiency, and quality ensures your product moves from concept to market with unmatched speed and precision.
WHITE PAPER
How can you tell if what you have is a tough cooling problem?
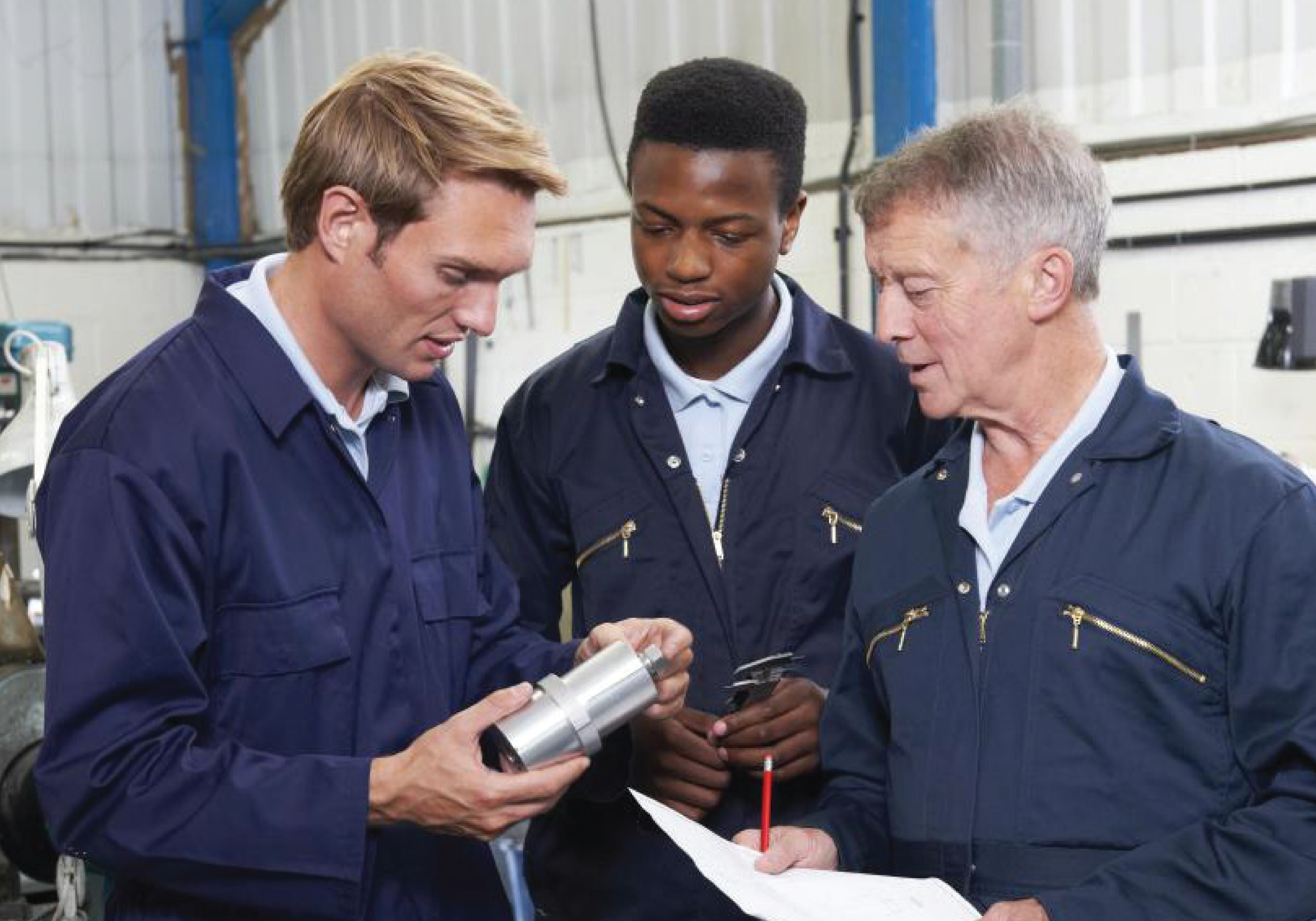
Achieving the lowest possible cycle times in a given project is like finding the holy grail in plastic injection molding. At Atalys, we have developed a method for estimating the optimum cure time (which is the largest component of cycle time) for each molding assignment. In essence, the model allows us to quantify the cooling challenge to be overcome, and enables us to determine the key parameters of the mold design that would be necessary if the desired cure time is to be achieved.
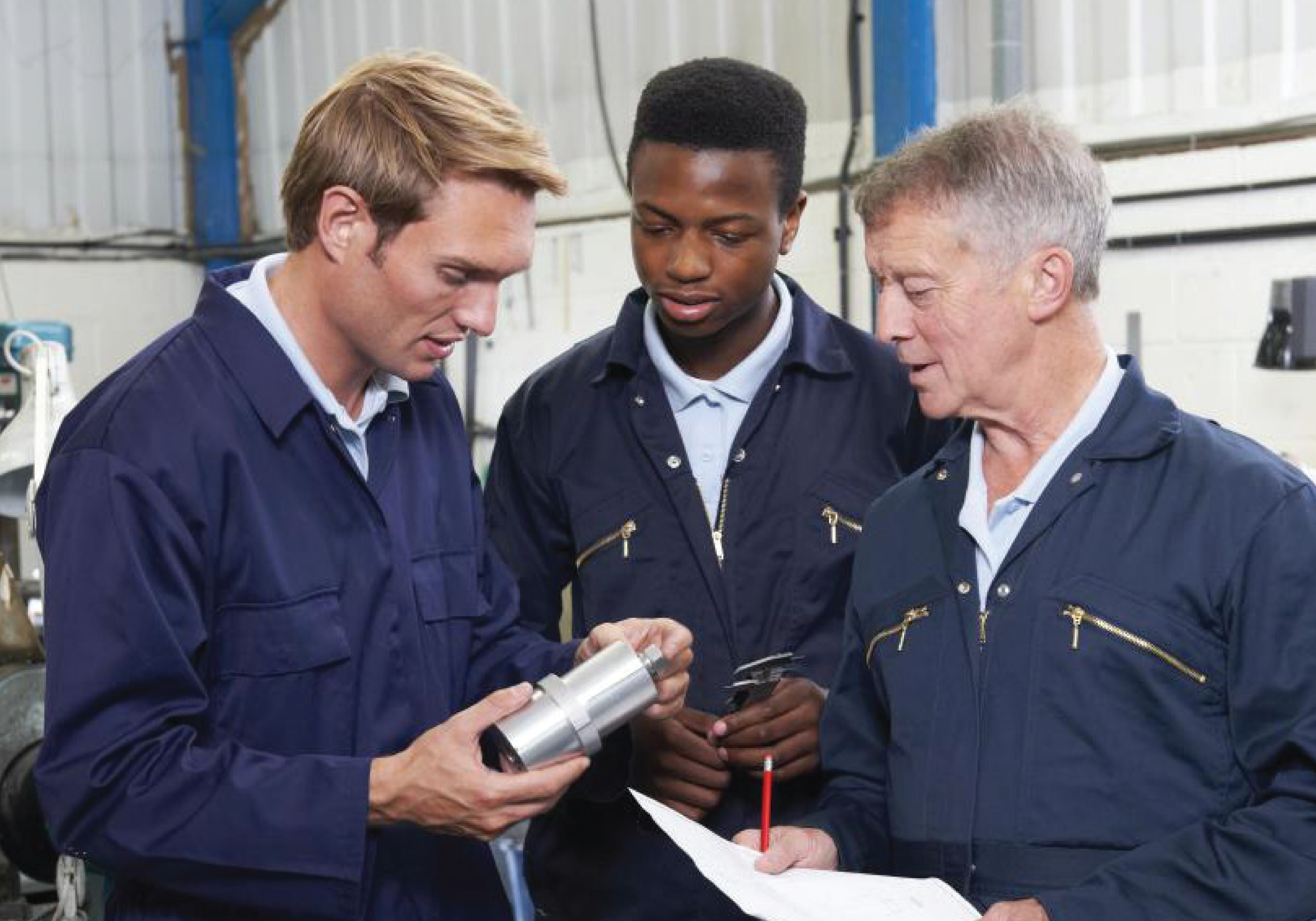
Learn more
Latest From Our Resource Center
Accelerating Cycle Times for Medical Device Manufacturing
Efficient thermal management is crucial in the production of medical devices and drug delivery systems, where up to 80% of the injection molding cycle is consumed by cooling. This Atalys presentation at SPE/MPD's Minitec at MD&M West in Anaheim California introduces a robust methodology for designing cooling systems using steady-state response thermal models, aimed at significantly reducing cooling times and boosting manufacturing efficiency. By precisely quantifying cooling challenges and optimizing key design parameters, this approach provides a streamlined modeling strategy for rapid and effective analysis.
Optimizing Mold Cooling for Medical Plastics: Insights from a Leading Expert
In this exclusive interview, Dr. Crispino explores the science behind cure time optimization, advanced thermal management, and the latest cooling methods to ensure precision and efficiency in medical device manufacturing. Learn about innovative modeling techniques, materials analysis, and actionable insights that can transform your mold design process. Ideal for professionals in engineering, R&D, manufacturing, and procurement, this interview provides insights into how you can improve cycle times and product quality.
The Power of Plastic Injection Molding: Why It’s the Ideal Choice for Medical Device Companies
The medical device industry is constantly evolving, driven by the demand for innovative solutions to improve patient outcomes and streamline healthcare processes. In this highly regulated and competitive environment, manufacturers must rely on advanced manufacturing techniques to produce high-quality, reliable, and cost-effective products.