Insights from the Forefront of Medical Device Manufacturing Innovation
Explore the latest trends, issues, and advancements in plastic injection molding and tooling for advanced medical devices.
ARTICLE
Atalys Expands Manufacturing Facility in the Dominican Republic
The new adjacent building adds 32,000 square feet of manufacturing capacity and value-added operations to the existing site. Atalys Dominican Republic is located within Las Americas Free Zone Park, a high-tech tax-free zone that is located less than 15 miles from a full-service port with excellent transportation and logistics infrastructure.
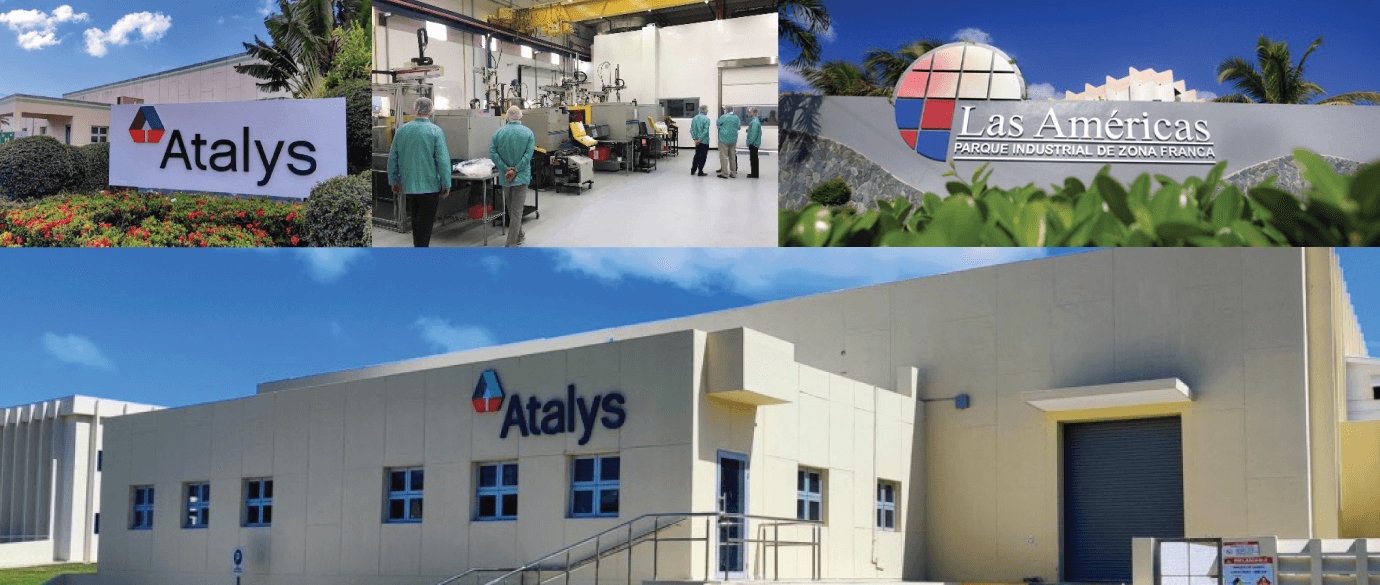
Earlier this year, we announced a significant expansion of our operations in the Dominican Republic. Specifically, we are tripling the size of our existing facility from 15,000 to 47,000 square feet through the addition of a new 32,000 square foot building adjacent to the current premises.
This expansion enables the company to significantly ramp up its production capacity and capabilities, accommodating more medical device customers and achieving greater operational efficiencies to address the growing needs of the medical device market. With this addition, Atalys offers in-country OEMs expanded local manufacturing alternatives while providing extremely competitive nearshore/low cost options for those companies that presently do not have this capability.
The new building will be dedicated to manual assembly operations with complementary processes of injection molding, pad printing, major tool repairs, and warehousing. Meanwhile, the existing facility will become the company’s primary plastics processing site focused on clean room injection molding as well as secondary operations such as testing and packaging.
“This expansion marks a significant milestone in our company’s history. With the addition of the new facility, we are poised to substantially increase our production capacity which will allow us to meet the growing demands of our customers more efficiently and effectively. The Dominican Republic has been an excellent location for our operations, offering a skilled workforce and a supportive business environment. This expansion is a testament to our commitment to this region and our confidence in its continued growth,” said Vinc Ellerbrock, President and CEO.
The new facility will not only enhance the company’s manufacturing capabilities but also bring about several key benefits. With dedicated areas for assembly, tool repair, and warehousing, the new facility will be designed for optimal workflow, leading to greater cost efficiencies and scalability in operations. The new building will also feature state-of-the-art equipment for some injection molding and pad printing, ensuring high-quality production standards. This expansion will also contribute to the local economy by creating new job opportunities in the region.
“We’re extremely proud of the team we have built in the Dominican Republic and this expansion reflects their hard work and dedication. The new facility with its advanced technologies and expanded capabilities will enable us to enhance our service offerings, improve turnaround times, and continue delivering exceptional quality products to our customers,” Mr. Ellerbrock added.
“Atalys is committed to maintaining the highest standards of quality and efficiency in its manufacturing processes. This expansion is aligned with our vision and mission of being at the forefront of innovation in the medical device manufacturing industry,” he concluded.
Share This Article
LEARN MORE
Latest from Our Resource Center
Accelerating Cycle Times for Medical Device Manufacturing
Efficient thermal management is crucial in the production of medical devices and drug delivery systems, where up to 80% of the injection molding cycle is consumed by cooling. This Atalys presentation at SPE/MPD's Minitec at MD&M West in Anaheim California introduces a robust methodology for designing cooling systems using steady-state response thermal models, aimed at significantly reducing cooling times and boosting manufacturing efficiency. By precisely quantifying cooling challenges and optimizing key design parameters, this approach provides a streamlined modeling strategy for rapid and effective analysis.
Optimizing Mold Cooling for Medical Plastics: Insights from a Leading Expert
In this exclusive interview, Dr. Crispino explores the science behind cure time optimization, advanced thermal management, and the latest cooling methods to ensure precision and efficiency in medical device manufacturing. Learn about innovative modeling techniques, materials analysis, and actionable insights that can transform your mold design process. Ideal for professionals in engineering, R&D, manufacturing, and procurement, this interview provides insights into how you can improve cycle times and product quality.
Optimizing Supply Chain Resilience in Robotic-Assisted Surgery Device Manufacturing
Whether you are an emerging robotic-assisted surgery company bringing new technologies to market, or looking to accelerate production or transitioning from prototype to full-scale manufacturing, Atalys is your strategic partner in navigating complex global supply chains and ensuring your precision components are not only delivered on time, but more importantly manufactured according to your specifications.