Insights from the Forefront of Medical Device Manufacturing Innovation
Explore the latest trends, issues, and advancements in plastic injection molding and tooling for advanced medical devices.
ARTICLE
Elevating the Future of Medical Device Manufacturing
With the acquisition of Schnipke Precision Molding, Atalys deepens its core competencies—in extreme precision tooling, optimized plastics processing and molding, and automated components assembly—further extending its leadership in minimally invasive and robotic assisted surgery, surgical access, instruments, energy, and drug delivery markets.
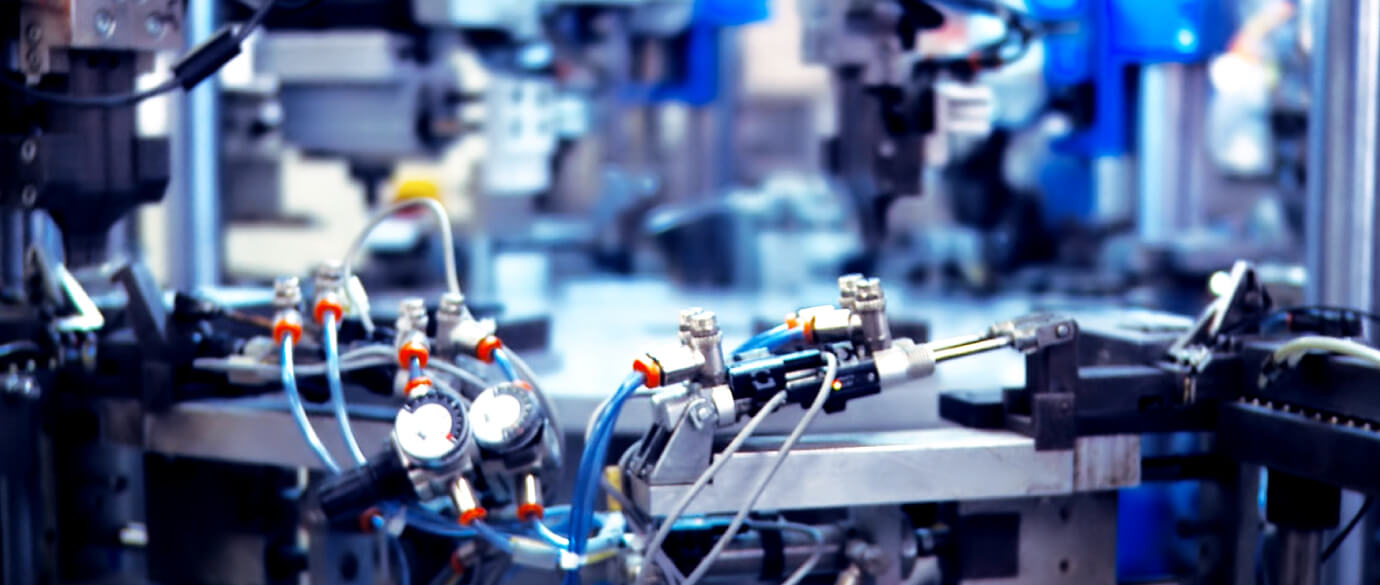
In the rapidly evolving world of medical device manufacturing, it is quite exhilarating to witness transformative moments that reshape our industry. Today, we shared a significant development at our company that marks a leap forward in our journey and reinforces our commitment to driving innovation and excellence in healthcare.
On April 5, 2024, we completed the acquisition of Schnipke Engraving Co., LLC (“Schnipke”), a leading manufacturer of plastic injection molded components for some of the world’s biggest names in medical devices. Throughout its more than 50-year history, Schnipke has established a formidable reputation as one of the pioneers in component manufacturing for highly intricate medical devices. Founded in 1967, Schnipke builds most of its production tools in-house with a team of highly experienced mold makers and engineers dedicated to crafting highly precise molds for the most demanding medical applications.
The decision to acquire Schnipke was driven by a shared vision and complementary strengths. Like us, Schnipke is a leader in the medical device manufacturing industry, renowned for its expertise, innovation, and commitment to quality. With Schnipke, we’re taking a bold step towards realizing our potential for even greater impact and success in revolutionizing medical device manufacturing.
By integrating Schnipke into Atalys, we gain not only their expertise and capabilities but also an organization that shares our passion for making a difference in the world. As a unified entity, we’re poised to further our leadership in multiple markets not just by meeting the needs of our customers, but by setting new standards and driving advancements in healthcare, through:
- Enhanced Capabilities: The integration of Schnipke’s unique strengths, especially in precision tooling, micro molding, and advanced automation capabilities, positions us at the forefront of innovation in the medical device market.
- Expanded Reach: With two additional manufacturing sites in Ottoville, Ohio and Tucson, Arizona, we’re not only boosting our production capacity but also extending our geographical footprint with a more robust manufacturing platform to serve customers, driving growth in important and major surgical markets.
- Shared Expertise: The collective knowledge and experience of our combined teams will continue to fuel innovation, improve efficiency, and enhance our ability to solve complex challenges for our customers, opening a world of possibilities for scalable, long-term growth.
With a focus on innovation, quality, and continuous improvement, this acquisition propels us to new heights, enabling us to offer groundbreaking solutions that power medical advancements in robotic-assisted and minimally invasive surgeries through lifesaving and market-leading components in surgical stapling, access, instruments, drug delivery, vessel sealing and surgical energy.
As Vinc Ellerbrock, President and CEO of Atalys, remarked, “Our acquisition of Schnipke represents a leap towards the future of medical device manufacturing. By integrating our highly proprietary technologies and advanced automation capabilities, we’re positioned to set revolutionary standards in efficiency and precision. By combining our strengths, we’re able to deliver a broader range of services and deeper technical expertise, all underpinned by an unwavering commitment to quality, customer satisfaction, and better health outcomes.”
“This strategic expansion is more than just a milestone for us; it’s a testament to our unwavering dedication to a brighter vision for healthcare. Together, we’re setting new benchmarks for precision, quality, and performance in medical device manufacturing,” added John Hoskins, Chief Commercial and Technology Officer of Atalys. He further noted that “as we embark on this exciting new chapter, our focus remains steadfast in building a heathier world through highly-engineered patient focused technologies that alleviate pain, save lives, and expand access to better health. We’re excited about continuing to redefine what’s possible in medical device manufacturing, driven by a shared belief in the power of technology and manufacturing quality to create a healthier future for all.”
Join us in celebrating this pivotal moment as we continue to push the boundaries of medical technology, driving forward with our commitment to excellence and innovation in everything we do.
Share This Article
LEARN MORE
Latest from Our Resource Center
Accelerating Cycle Times for Medical Device Manufacturing
Efficient thermal management is crucial in the production of medical devices and drug delivery systems, where up to 80% of the injection molding cycle is consumed by cooling. This Atalys presentation at SPE/MPD's Minitec at MD&M West in Anaheim California introduces a robust methodology for designing cooling systems using steady-state response thermal models, aimed at significantly reducing cooling times and boosting manufacturing efficiency. By precisely quantifying cooling challenges and optimizing key design parameters, this approach provides a streamlined modeling strategy for rapid and effective analysis.
Optimizing Mold Cooling for Medical Plastics: Insights from a Leading Expert
In this exclusive interview, Dr. Crispino explores the science behind cure time optimization, advanced thermal management, and the latest cooling methods to ensure precision and efficiency in medical device manufacturing. Learn about innovative modeling techniques, materials analysis, and actionable insights that can transform your mold design process. Ideal for professionals in engineering, R&D, manufacturing, and procurement, this interview provides insights into how you can improve cycle times and product quality.
Optimizing Supply Chain Resilience in Robotic-Assisted Surgery Device Manufacturing
Whether you are an emerging robotic-assisted surgery company bringing new technologies to market, or looking to accelerate production or transitioning from prototype to full-scale manufacturing, Atalys is your strategic partner in navigating complex global supply chains and ensuring your precision components are not only delivered on time, but more importantly manufactured according to your specifications.