Insights from the Forefront of Medical Device Manufacturing Innovation
Explore the latest trends, issues, and advancements in plastic injection molding and tooling for advanced medical devices.
ARTICLE
The Power of Plastic Injection Molding: Why It’s the Ideal Choice for Medical Device Companies
The medical device industry is constantly evolving, driven by the demand for innovative solutions to improve patient outcomes and streamline healthcare processes. In this highly regulated and competitive environment, manufacturers must rely on advanced manufacturing techniques to produce high-quality, reliable, and cost-effective products.
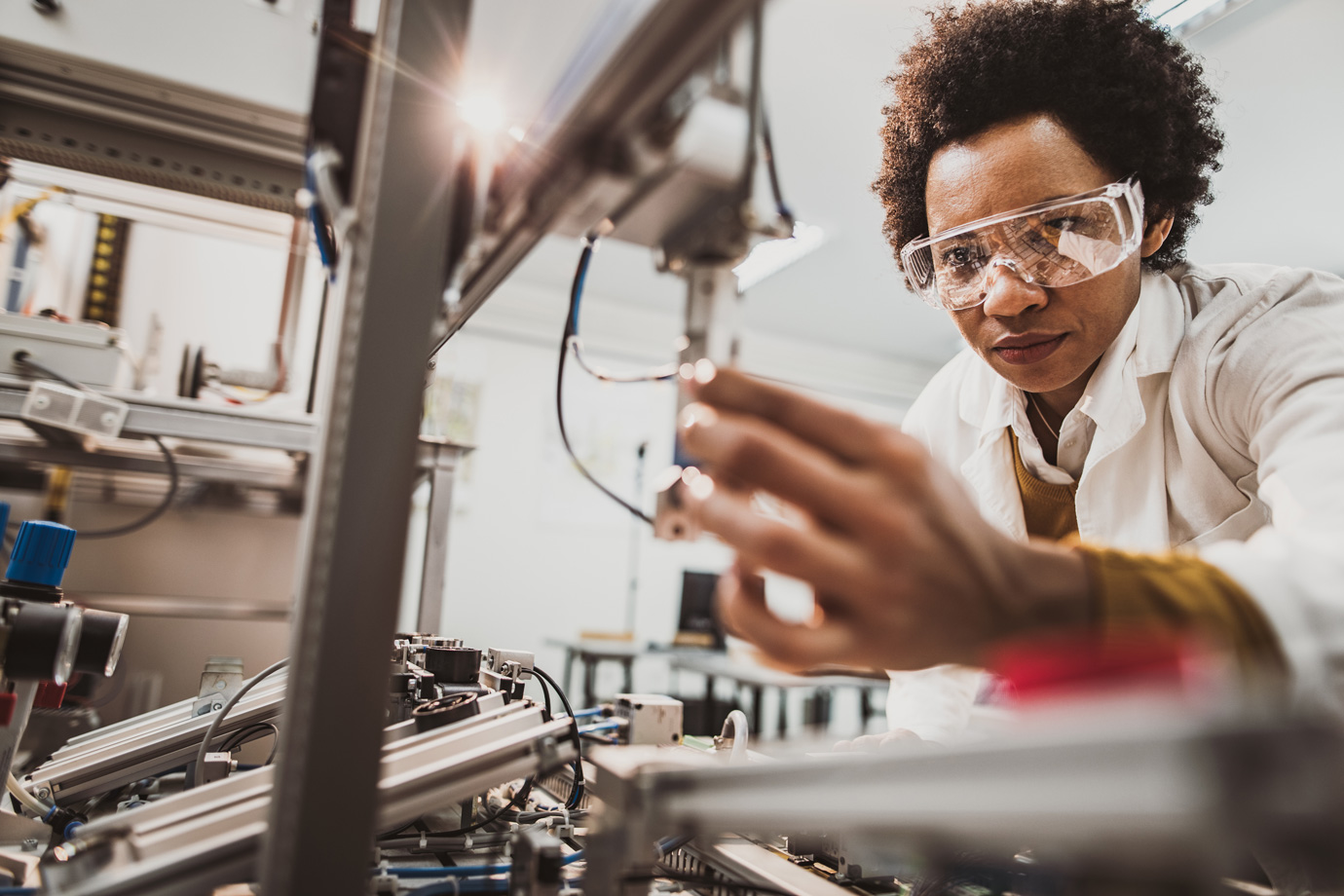
The relentless pursuit of excellence in the medical device industry is shaping a future where innovation, precision, and cost-efficiency are not just desired but expected. Fueled by the necessity for groundbreaking solutions that enhance patient care and optimize healthcare procedures, the industry finds itself in a dynamic and demanding landscape. Amid this complexity, manufacturers are turning to sophisticated manufacturing techniques to craft products that are not only reliable and high-quality but also economically viable. At the heart of this technological revolution lies plastic injection molding—an adaptable and proficient process that has solidified its role as an essential technique in medical device fabrication. In this article, we delve into the multifaceted advantages of plastic injection molding, illuminating why it stands as the favored method for medical device manufacturers and how it acts as a catalyst in transforming healthcare today.
Design Flexibility
One of the main advantages of plastic injection molding is its ability to produce complex, intricate parts with ease. This design flexibility allows medical device manufacturers to create products with unique geometries and features that would be difficult, if not impossible, to achieve using other manufacturing methods. This is due to the flexibility of the mold design, which can be customized to fit the unique requirements of each part. Injection molding also allows for the use of a wide range of materials, including thermoplastics, thermosets, and elastomers, which enables medical device manufacturers to create parts with a variety of properties, such as rigidity, flexibility, and transparency.
High Precision and Tight Tolerances
Precision and accuracy are critical in the medical device industry, as even minor deviations from the intended design can have serious consequences for patient safety and device performance. Plastic injection molding is well-suited for producing high-precision parts with tight tolerances, thanks to its ability to consistently replicate complex geometries and maintain tight process control. Advanced molding machines and tooling technologies further enhance this precision, enabling the production of components with tolerances in the range of a few microns. Additionally, the use of high-quality molds and materials ensures that the parts produced are of the highest quality and meet the strict requirements of the medical device industry.
Scalability and High-Volume Production
Plastic injection molding is an ideal choice for high-volume production, as it offers significant economies of scale. It is a highly controlled process that produces high-quality parts with consistent and repeatable results. The process is highly automated, which allows for rapid production rates and consistent part quality, even when manufacturing thousands or millions of identical components. This scalability is particularly advantageous for medical device manufacturers, as it enables them to meet the growing demand for their products while maintaining strict quality standards. Injection molding also allows for quick turnaround times, which enables medical device manufacturers to respond quickly to changes in demand or design requirements.
Material Selection and Biocompatibility
The medical device industry requires materials that are not only strong and durable but also biocompatible, ensuring they do not cause adverse reactions when in contact with the human body. Plastic injection molding is compatible with a wide range of biocompatible resins, such as PEEK, PEI, PPSU, and PC, which offer excellent mechanical properties such as chemical resistance, transparency, flexibility, or biocompatibility. This material versatility allows medical device manufacturers to select the most suitable material for their specific application, ensuring optimal performance and patient safety.
Cost-Effectiveness
Plastic injection molding is a cost-effective manufacturing method for medical device parts and components. The process of injection molding allows for high-volume production of parts, which reduces the overall cost per unit. It is also highly automated, which helps to reduce labor costs and minimize the risk of human error. Additionally, the use of multi-cavity molds allows for the simultaneous production of multiple parts, further improving efficiency and reducing overall production costs. The high degree of repeatability and low scrap rates associated with injection molding also contribute to a more cost-effective manufacturing process.
Reduced Assembly and Secondary Operations
Plastic injection molding can produce parts with high levels of precision and accuracy, which minimizes the need for secondary operations which further reduces costs. Many injection-molded parts can also be designed to incorporate features such as snap-fits, interlocking joints, or hinges, which can help reduce or eliminate the need for assembly and secondary operations like bonding or welding. This can lead to reduced production times, lower labor costs, and improved part quality.
Integration of Multi-Material and Multi-Color Components
In some cases, medical devices may require the integration of multiple materials or colors in a single component. Plastic injection molding is well-suited for this purpose, as techniques such as two-shot molding, overmolding, and insert molding enable the production of multi-material and multi-color parts in a single manufacturing step. This integration can lead to improved part quality, reduced assembly time, and enhanced design flexibility.
Consistent Quality
The high degree of process control and repeatability in plastic injection molding ensures consistent part quality across large production runs. This is particularly important in the medical device industry, where consistent performance and reliability are essential for patient safety and device efficacy. With plastic injection molding, manufacturers can achieve a high level of consistency and quality control, thanks to the precision and repeatability of the process. By using automated inspection and quality control systems, manufacturers can ensure that every part produced meets the required specifications and standards.
Through its closed mold system and automated handling processes, plastic injection molding manufacturers can produce parts in a clean and controlled environment, minimizing the risk of contamination or impurities. Plastic injection molding is also capable of producing parts with a high-quality surface finish and appearance, often requiring little or no post-processing. All of these are particularly important in the medical device industry, where cleanliness, sterility, and aesthetics are critical factors and play a role in patient well-being and safety.
Reduced Time-to-Market
Another advantage of plastic injection molding is its ability to produce high volumes of parts quickly and efficiently, which can help reduce time-to-market for new medical devices. With modern injection molding machines and automation technologies, it is possible to produce parts in large quantities with minimal human intervention, allowing manufacturers to ramp up production quickly and efficiently. Injection molding allows for the rapid creation of prototypes and the development of production tooling, enabling medical device manufacturers to quickly iterate their designs and bring new products to market faster. This agility is crucial in the fast-paced medical device industry, where the ability to respond quickly to market demands and regulatory changes can provide a significant competitive advantage.
Environmental Sustainability
The medical device industry is increasingly focused on sustainability, and plastic injection molding can play a role in reducing environmental impact. Injection molding produces very little waste, as any excess plastic can be recycled and reused. The process also uses energy-efficient machinery and requires minimal energy to produce each part, which reduces the overall carbon footprint of the manufacturing process. Additionally, many of the materials used in plastic injection molding are biocompatible and can be safely disposed of, reducing the risk of environmental harm, and enhancing the overall sustainability of medical device manufacturing.
Innovating to Deliver Cutting-Edge Solutions
Plastic injection molding is a powerful manufacturing technique that offers numerous benefits for medical device manufacturers. Its ability to produce high-precision, complex parts in a cost-effective manner makes it the ideal choice for the production of medical device components. With the wide range of biocompatible materials available, manufacturers can ensure optimal performance and patient safety for their products. Additionally, the scalability of the process allows companies to meet the growing demand for their devices while maintaining strict quality standards. Furthermore, the ability to integrate multi-material and multi-color components in a single manufacturing step offers enhanced design flexibility and reduces assembly time.
As the medical device industry continues to evolve and innovate, plastic injection molding will remain a key manufacturing method, helping manufacturers deliver cutting-edge solutions that improve patient care and streamline healthcare processes. By staying informed about the latest advancements in plastic injection molding technology and collaborating with experienced partners, medical device manufacturers can harness the full potential of this powerful manufacturing technique. As a result, they will be well-positioned to develop innovative, high-quality, and cost-effective products that improve patient care and support the ever-changing needs of the healthcare industry.
Share This Article
LEARN MORE
Latest from Our Resource Center
Accelerating Cycle Times for Medical Device Manufacturing
Efficient thermal management is crucial in the production of medical devices and drug delivery systems, where up to 80% of the injection molding cycle is consumed by cooling. This Atalys presentation at SPE/MPD's Minitec at MD&M West in Anaheim California introduces a robust methodology for designing cooling systems using steady-state response thermal models, aimed at significantly reducing cooling times and boosting manufacturing efficiency. By precisely quantifying cooling challenges and optimizing key design parameters, this approach provides a streamlined modeling strategy for rapid and effective analysis.
Optimizing Mold Cooling for Medical Plastics: Insights from a Leading Expert
In this exclusive interview, Dr. Crispino explores the science behind cure time optimization, advanced thermal management, and the latest cooling methods to ensure precision and efficiency in medical device manufacturing. Learn about innovative modeling techniques, materials analysis, and actionable insights that can transform your mold design process. Ideal for professionals in engineering, R&D, manufacturing, and procurement, this interview provides insights into how you can improve cycle times and product quality.
Optimizing Supply Chain Resilience in Robotic-Assisted Surgery Device Manufacturing
Whether you are an emerging robotic-assisted surgery company bringing new technologies to market, or looking to accelerate production or transitioning from prototype to full-scale manufacturing, Atalys is your strategic partner in navigating complex global supply chains and ensuring your precision components are not only delivered on time, but more importantly manufactured according to your specifications.